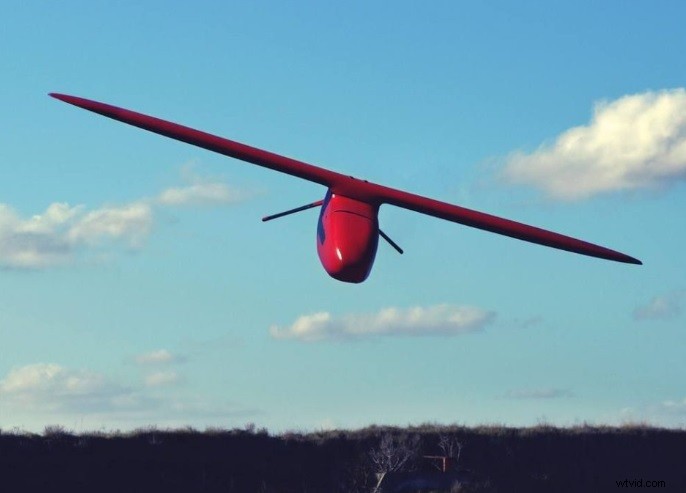
UAV-casco's verwijzen naar de fysieke hoofdstructuur van een onbemand luchtvoertuig of drone, waarop alle vitale componenten zoals elektronische systemen, nuttige ladingen en motoren zijn geïnstalleerd.
De kwaliteit van casco's is afhankelijk van de aard van de missie, het gewicht van de lading die het moet dragen en de start- en landingsbenadering van de drone. Hoge sterkte met een minimaal mogelijk gewicht, groot laadvermogen, uitstekende manoeuvreerbaarheid en hoge zweefefficiëntie zijn de essentiële vereisten van alle casco's. Militaire UAV's hebben een hoog uithoudingsvermogen nodig om lange tijd in de lucht te blijven.
Alle moderne drones zijn uitgerust met een reeks sensoren en andere systemen, waardoor het totale gewicht onvermijdelijk toeneemt en de vliegtijd wordt verkort.
Gewichtsvermindering is daarom van cruciaal belang en om de casco's te bouwen, gebruiken fabrikanten tegenwoordig niet-conventionele materialen zoals composieten (meestal gemaakt met vezels en harsen), die het gewicht van UAV's verminderen zonder afbreuk te doen aan hun sterkte.
Er zijn enkele van de gebruikelijke materialen en composieten die worden gebruikt voor UAV-casco's:
1. Kunststof
Kunststof is gemakkelijk te vormen tot vaste objecten van verschillende groottes en vormen. Kunststof is lichter dan metaallegeringen, heeft hoge kneedbare eigenschappen en biedt een hoge weerstand tegen corrosie en chemicaliën. Het heeft ook een lage elektrische en thermische geleidbaarheid en een uitstekende duurzaamheid en een hoge sterkte-gewichtsverhouding. Kunststof is zeer kostenbesparend. Propellers en skids van een drone zijn meestal gemaakt van plastic.
2. Aluminiumlegeringen
Aluminium is een veelgebruikt metaal dat wordt gebruikt om drone-casco's te bouwen. Bekend om zijn lage dichtheid en hoge sterkte, zijn aluminiumlegeringen bestand tegen corrosie door passivering, waardoor het een ideale keuze is voor de lucht- en ruimtevaartindustrie.
3. Composieten
Vergeleken met aluminium verminderen composieten het gewicht met 15-45%. Naast hoge sterkte zijn composieten bestand tegen corrosie door zout water en elektrolyse. In het geval van vogelaanvaringen of ongevallen, absorberen ze de impactenergie, in plaats van deze naar de lagere eenheden te verplaatsen. Ze produceren minder geluid of trillingen in tegenstelling tot aluminium of andere metalen.
Enkele van de conventionele composieten die voor casco's worden gebruikt, zijn koolstofvezelversterkte polymeren (CFRP), glasvezelversterkte polymeren (GFRP), boorvezelversterkte polymeren (BFRP) en aramidevezelversterkte polymeren (AFRP).
a. Met koolstofvezel versterkte polymeren (CFRP)
Koolstofvezel is een combinatie van koolstofvezels en thermohardende harsen en biedt gewichtsvermindering, sterkte, verbeterde duurzaamheid en lage thermische krimp. Voor het maken van koolstofvezel worden koolstofatomen evenwijdig aan de hoofdas van het filament uitgelijnd. Voor commercieel gebruik worden duizenden filamenten samen gewikkeld. Koolstofvezels zijn kosteneffectief, sterker dan staal, lichter dan aluminium en stijver dan titanium. Het kan gemakkelijk in massa worden geproduceerd. Hexcel Corporation is een van de toonaangevende spelers in de ontwikkeling van koolstofvezels. Ze maken HexTow-koolstofvezel door alle soorten thermohardende en thermoplastische harsen te combineren.
b. Glasvezelversterkte polymeren (GFRP)
Het op één na meest gebruikte materiaal in casco's, glasvezel, biedt een lage materiaalrek en een hoge materiaalsterkte. Bovendien is het gemakkelijk te produceren en vraagt het weinig onderhoud. Glasvezel is geschikt voor een verscheidenheid aan toepassingen vanwege de hoge sterkte, verhoogde flexibiliteit, lange duurzaamheid, uitstekende stabiliteit en hoge weerstand tegen hitte, temperatuur en vocht. Het is lichtgewicht en kan worden gevormd om radomes en antennesubstraten te ontwerpen. Owens Corning (VS) is een van de toonaangevende spelers op het gebied van glasvezelversterkte polymeren. Andere toonaangevende fabrikanten zijn Jushi Group (China), Owens Corning (VS), Taishan Fiberglass Inc. (China), CPIC (China), Saint-Gobain Vertex (Frankrijk), Nippon Sheet Glass (Japan) en Johns Manville (VS) , onder andere.
c. Met boorvezel versterkte polymeren (BFRP)
Boorvezel is het sterkste en duurste materiaal dat in de handel verkrijgbaar is voor casco's. BFRP wordt gebruikt in F-15-jagers, B-1-bommenwerpers, Black Hawk-helikopters, spaceshuttles en Predator, vanwege de uitstekende druksterkte. Dit polymeer heeft zes keer meer elasticiteitsmodulus in vergelijking met GFRP. Boorvezel wordt gebruikt in de Amerikaanse militaire vliegtuigen zoals F-14 en F-15. De beperkte toepassing van boorvezels wordt toegeschreven aan de toxische aard, hoge kosten en verhoogde brosheid in vergelijking met andere vezels. Het heeft niet de voorkeur voor grond- en onderwatervoertuigen. Specialty Materials, Inc. is een toonaangevende fabrikant van boorvezelproducten.
Aramidevezelversterkt polymeer.
d. Aramidevezelversterkt polymeer (AFRP)
Aramidevezel is een synthetische vezel die een hoge slagvastheid en verhoogde stijfheid biedt. Het snijden van AFRP vereist een hoge nauwkeurigheid en precisie, waardoor ze duur en moeilijk te gebruiken zijn. Aramidevezel is bekend in verschillende handelsnamen zoals Nomex (een meta-aramide) of Kevlar (een para-aramide). Het wordt veel gebruikt voor militaire ballistiek en kogelvrije vesten, vanwege de gevoeligheid voor licht, compressie en hygroscopie. Kevlar en Twaron zijn de twee meest populaire aramidevezels. Ze worden gebruikt in vliegtuigonderdelen, helikopters, ruimtevoertuigen, raketten, kano's, kajaks, motorboten, remmen, koppelingen, enz.
Dit zijn enkele van de belangrijkste voordelen van het gebruik van composieten voor UAV-casco's in plaats van metalen:
- lichtgewicht, waardoor de drone energiezuinig is
- ongelooflijk sterk en moest heel erg breken
- weerstand tegen corrosie en compressie
- lage bewerkingsfouten
- ontwerpflexibiliteit. Makkelijk ingewikkelde onderdelen te fabriceren
- maximale stijfheid en sterkte
- minder aantal assemblages en bevestigingsmiddelen
- hogere 'stealth'-mogelijkheden met lage radar- en microgolfabsorptie
- lage thermische uitzetting bij vluchten op grote hoogte
- weinig onderhoud
Composieten hebben ook enkele nadelen ten opzichte van metalen. Dit zijn:
- duur om te bouwen
- structurele degradatie bij hoge temperaturen en natte omstandigheden
- delaminatie en scheuren
- lage energieabsorptie, resulterend in hoge impact tijdens harde landing
- arbeidsintensief en complex fabricageproces
- hogere onderhoudskosten